INNOVATION STORIES
ENVIRONMENTAL MANAGEMENT
Contributing to the Environment while Achieving Business Growth
The Unique History of Konica Minolta’s Environmental Activities
- INDEX
“Environmental measures are costly.” Previously, this was the norm for many companies. We set and attained industry-leading ambitious targets one after another as we sought to contribute to corporate value through environmental activities. This eventually led to the idea of creating new value and changing society through environmental activities by collaborating with stakeholders, including suppliers and customers, beyond the scope of our responsibility.
Looking back on our history, we started to work on environmental activities decades ago. Konica, which was a chemical manufacturer whose product lineup included photographic films, was keen to tackle the problem of environmental pollution. In 1971, the company established an environmental department at each business site, and the following year, set up an environmental department at the head office. In 1992, Konica and Minolta products gained Blue Angel certification, an ecolabel of the German Federal Government known for rigorous certification standards, for the first time in the field of copiers. The initial objective of environmental measures was to comply with laws and regulations and meet standards. However, employees who considered that mere compliance was not enough embarked on new challenges. This marked the beginning of our unique approach.
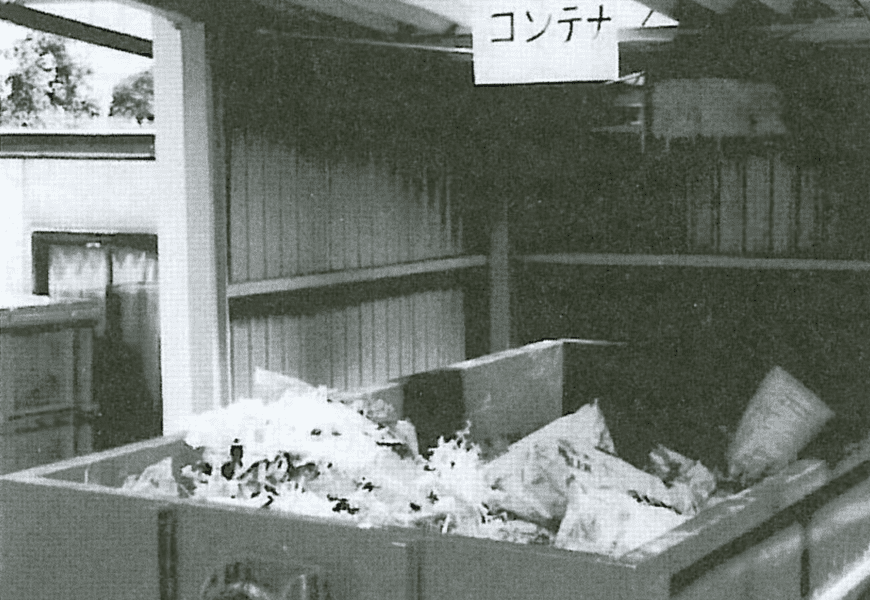

Reducing both waste and cost
by changing the way of thinking
Our environmental activities changed course significantly with the launch of zero-emission activities in 1999, which aim to minimize the quantity of landfill waste by recycling waste from production and reducing waste itself. At the time, many companies were working on zero-emission activities, but the main approach was to sort waste into different categories and then look for recycling companies. However, this was time-consuming and treatment was costly, and was a heavy burden for the company.
However, the person in charge who had just been assigned to the environment section came up with a new idea and focused on the treatment cost. “The production section is sensitive to costs, so they will surely cooperate with us if they know that reducing waste also reduces cost.” The environment section set the target of slashing the treatment cost by 90%. This was considered to be totally impossible, but the person in charge had a strategy: using the waste in-house would reduce waste, as well as reduce the quantity of newly purchased resources. With this approach, the target might just be attainable.
They first focused on the runners of molded parts at Yamanashi Konica, which manufactured camera parts. Runners are the frames that surround parts in plastic models, and serve as channels along which molten plastic flows during the molding of parts, so it is difficult to eliminate them. However, a study showed that, surprisingly, 50% of raw materials purchased was discarded as runners. Might it be possible to recycle the runners?

The question was how to maintain the quality at the same time. The plastic material contained glass fiber to increase the molding accuracy. The conventional wisdom was that crushing and melting the material for recycling would reduce the strength and accuracy of parts and cause product defects. However, giving up was not an option. The percentage of crushed runners mixed to ensure the necessary strength and accuracy was calculated, and experiments were conducted repeatedly using the actual production equipment at the plant after the end of daily work. As a result, it was found that runners could be mixed with virgin materials (new raw materials) in the ratio of 20:80 without any problem. Eventually, the recycling technology was successfully introduced in June 2001.
This accomplishment could not have been made without the help of engineers at the raw materials manufacturers. Recycling would reduce these manufacturers’ revenues from virgin materials. However, because we arranged to allow this know-how to be shared with other customers, the raw materials manufacturers understood that they would be able to differentiate themselves from their competitors.
Yamanashi Konica became the first zero-emission plant in Group and attracted much media attention. Inspired by the success of this project, other production sites started to express their intention to work on zero-emission activities. The production items and waste conditions varied at respective plants, and so different measures were needed. Various creative ideas were proposed, such as checking with suppliers whether delivered parts were overpackaged to eliminate waste and reviewing the cleaning procedure to reduce toner loss. By the end of FY2001, five sites had attained zero emissions.
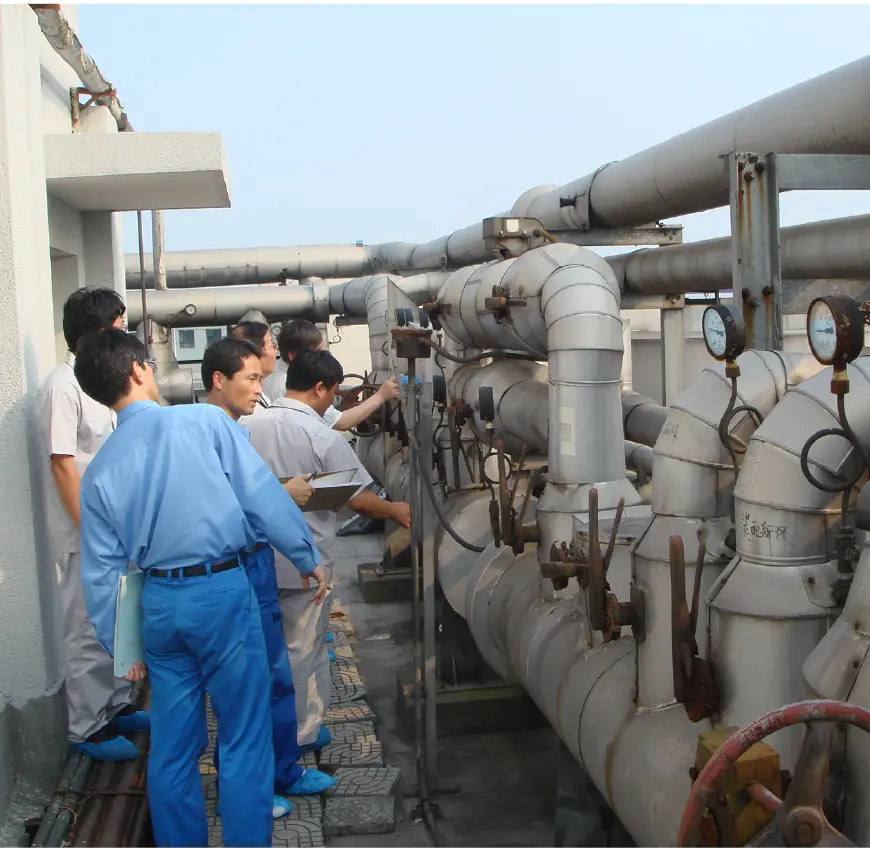
In 2005, after the management integration of Konica and Minolta, the activities were rolled out to production sites outside Japan. The personnel in charge of the environment kept visiting sites and offering assistance. In 2009, Level 2 zero emissions were finally attained at all production sites worldwide. When zero emissions were attained, the director in charge of the environment at the head office visited each site to award certification and shared the joy of the accomplishment. In 2010, these activities started to drive Konica Minolta’s environmental activities under the Green Factory certification system, including reducing CO2 emissions and chemical risks. The targets to be attained are reviewed in line with the Medium-term Business Plan every three years, and they have been raised continuously. Twenty-five years after launching the zero-emission activities, the practice of linking environmental initiatives with cost reduction is regarded as the norm and is well accepted around the world.
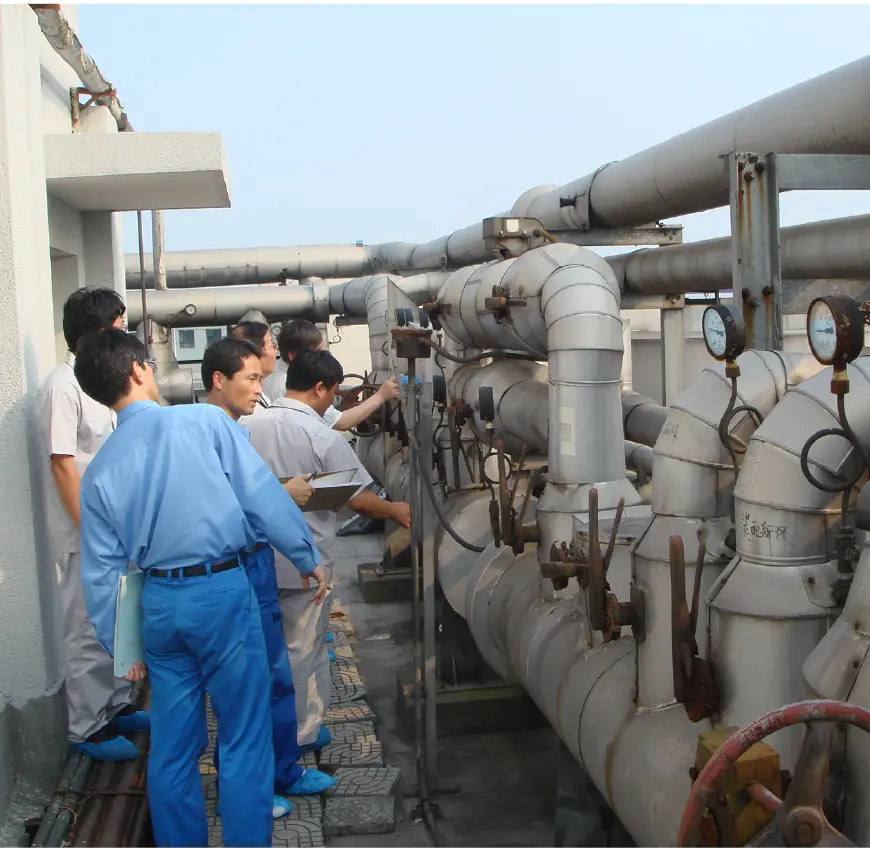
Steady results with a long-term vision
Another advanced initiative is Eco Vision 2050, which was announced in January 2009. This long-term environmental vision with the target year of 2050 aims to attain the three goals of preventing global warming, supporting a recycling-oriented society, and restoring and preserving biodiversity. The reduction of greenhouse gases was regarded as the most important mission with the aim of reducing CO2 emissions across the product lifecycle by 80% by 2050 compared to FY2005 levels. Back then, few companies mentioned such far-reaching and challenging targets. Besides, the financial crisis was reverberating around the world after the collapse of Lehman Brothers in September 2008. Some employees questioned why it was necessary to declare such a vision. However, the personnel in charge of the environment believed: “Ambitious targets cannot be attained only by adding up feasible numbers. We should set targets with a future vision and work based on backcasting.”
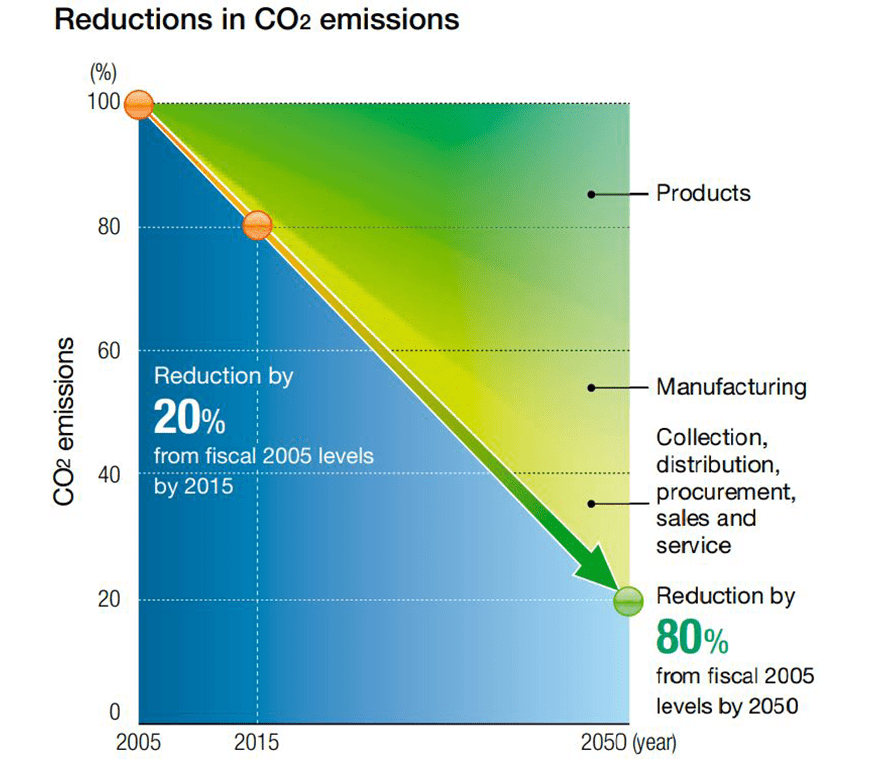
To attain the targets, it was essential to present convincing reasons and share values. We focused on the permissible amount of greenhouse gases absorbed by the natural environment of the planet, which had been stated by the Intergovernmental Panel on Climate Change (IPCC). The permissible amount, which is estimated at 11.4 billion tons in 2050, divided by the global population projected by the United Nations, which is 9.2 billion, yields a figure for permissible per capita emissions in 2050 of 1.24 tons. Meanwhile, the global emissions of greenhouse gases, which were 49 billion tons in 2004, divided by the global population, which was 6.4 billion, yields per capita emissions of 7.66 tons. This indicates that emissions must be reduced by 80%.
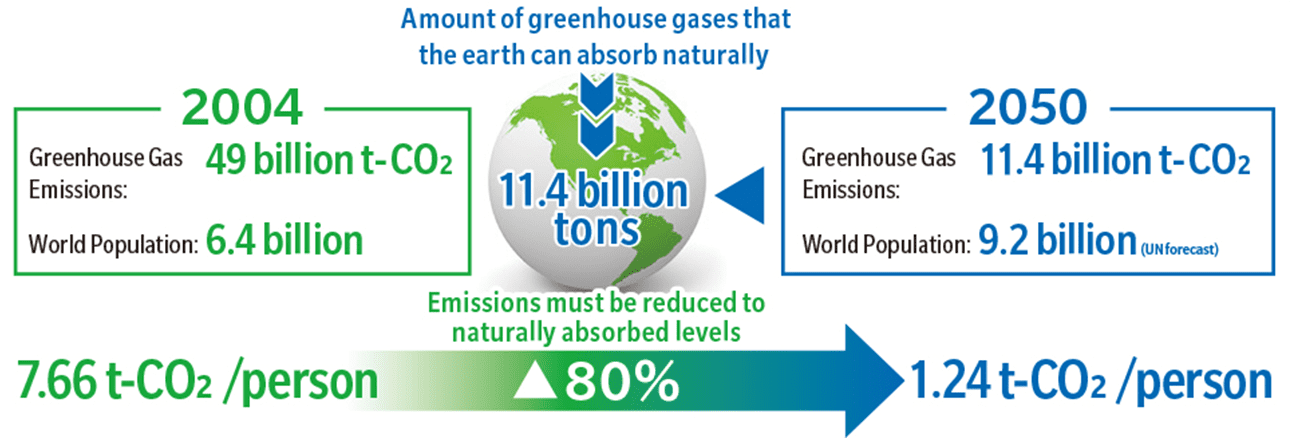
Eco Vision 2050 serves as the guidelines for Konica Minolta’s environmental activities. Good results have been produced steadily by formulating and implementing plans each year. By FY2022, a 58% reduction had been attained. The following year, the 2050 target was revised upward to a 100% reduction (net zero) from 80%. We continue taking on further challenges.
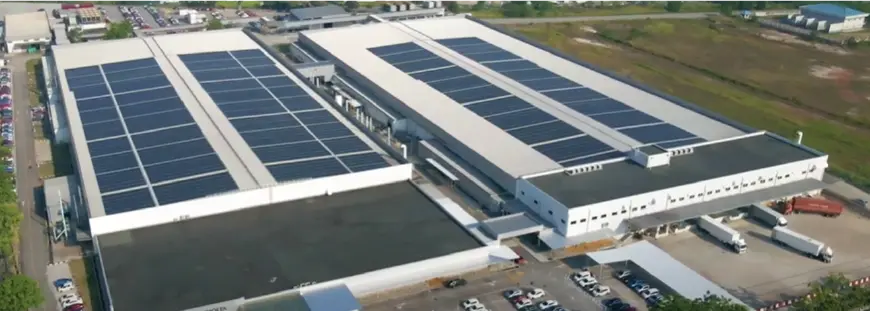
Creating environmental value beyond the company
Our environmental activities aim to solve social issues in collaboration with stakeholders beyond our in-house activities. The first activities were the Green Supplier Activities, which started in 2014. Our employees visited suppliers that delivered parts to our production sites in respective countries and made energy conservation assessments and offered improvement know-how. At first, suppliers were reluctant, but they began to accept our activities and became motivated to give it a try when we showed our track record in reducing both environmental impact and cost. Previously, the production and purchasing sections had supported suppliers in improving the quality, so this laid the groundwork to facilitate improvement activities through cooperation.
At first, the personnel in charge of the environment directly visited suppliers to make energy conservation assessments. On-site checks of the actual condition were useful, but the number of sites that could be checked was limited. Thus, a digital tool for automatically conducting assessments was developed to enable suppliers to make assessments, identify issues, and implement measures by themselves. The number of sites checked annually increased from three or four to about 10, and the activities spread rapidly. By 2022, the assessments had been conducted at about 50 suppliers, and the activities are expected to accelerate in the future.

In 2016, “Carbon Minus status” was set as a new commitment of Eco Vision 2050. We define Carbon Minus status as an initiative to create a state where the amount of CO2 reduction outside of our responsibility exceeds the amount of emissions. This means not only reducing CO2 emissions over the lifecycle of our products (purchasing of materials, production, logistics, sales and services, use of products by customers, and disposal) but also encouraging stakeholders, including suppliers and customers, to make reductions beyond the emissions from business activities, thereby reducing CO2 emissions from society as a whole.
One of such initiatives is the Green Marketing activity. Today, it is essential for every company and organization to implement environmental measures, but there are surely entities that cannot find effective solutions. Thus, we have been working to publicize our activities and track record at environmental seminars and to strengthen the relationship with customers based on close collaboration between the personnel in charge of the environment and sales by utilizing our environmental technologies and know-how in solving customers’ issues. We also aim to help solve environmental issues at customers through our business, such as reducing waste and energy consumption in the manufacturing process by shifting from analog to digital printing in the production print business, and applying hyperspectral imaging technology, which can identify the ingredients and characteristics of materials by capturing wavelengths invisible to the human eye, to automatic sorting of waste plastics in the recycling industry in the sensing business.
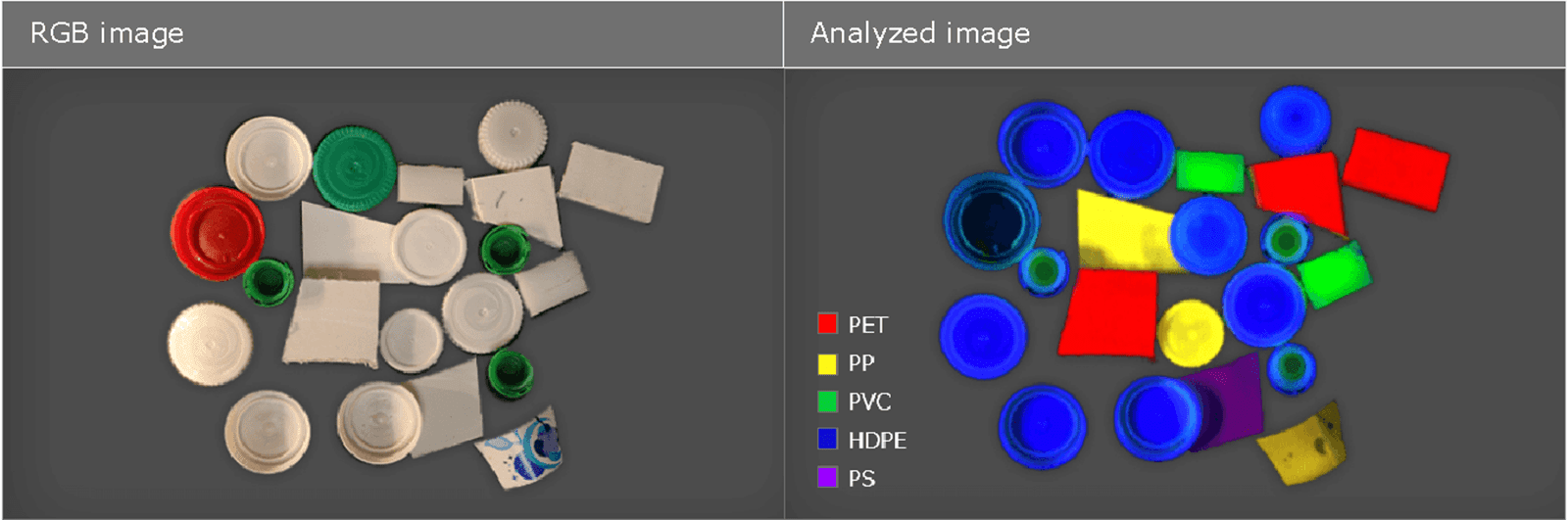
In addition, we launched the Environmental Digital Platform with 16 companies in Japan for co-creation across different business types in 2020. This initiative aims to evolve the environmental management of the entire industry through the sharing of environmental knowledge of participating companies and exchange of opinions at workshops. In 2023, the number of participating companies increased to 86, and the resources of many more companies are expected to create new value in the future.
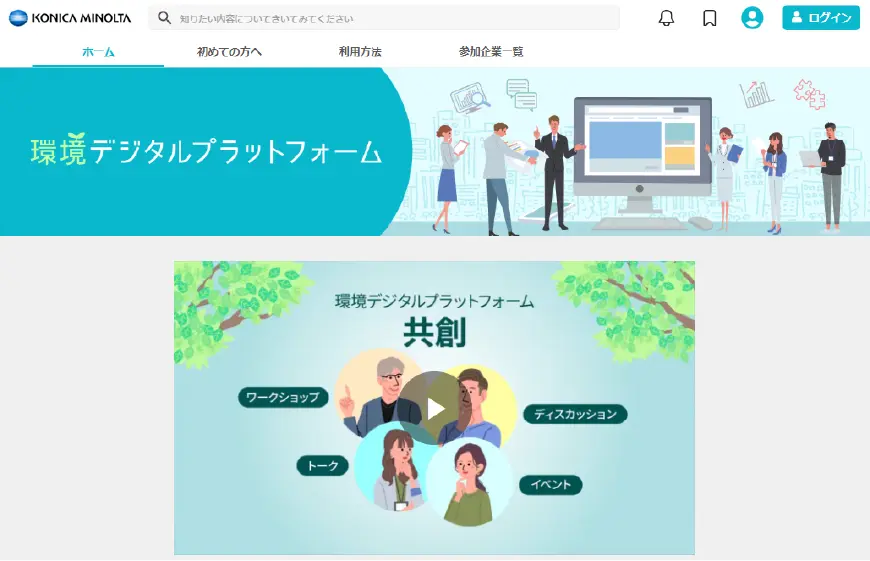
With society rapidly shifting to decarbonization and zero natural resources, Konica Minolta aims to realize a better society by creating environmental contributions that cannot be attained by us alone while pursuing both environmental activities and business growth.
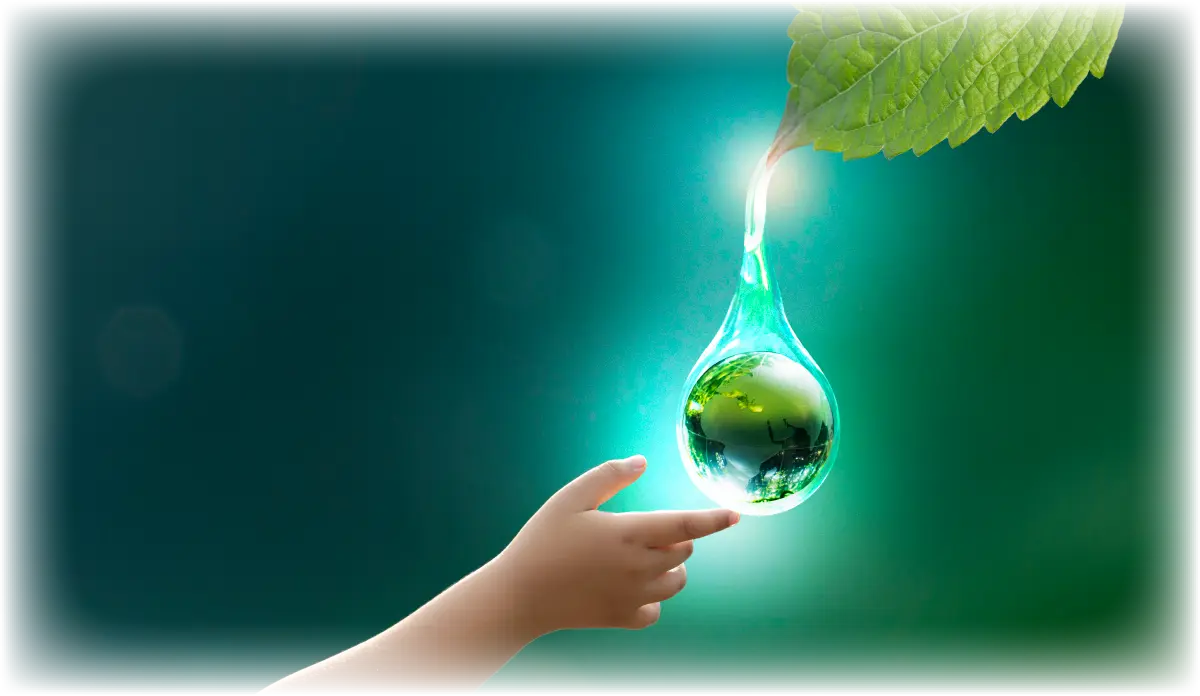
In the interest of clarity, “Konica” and “Minolta,”—the trade names that were used before the merger that formed “Konica Minolta”—are used throughout this text. Each company underwent a number of name changes throughout their history.
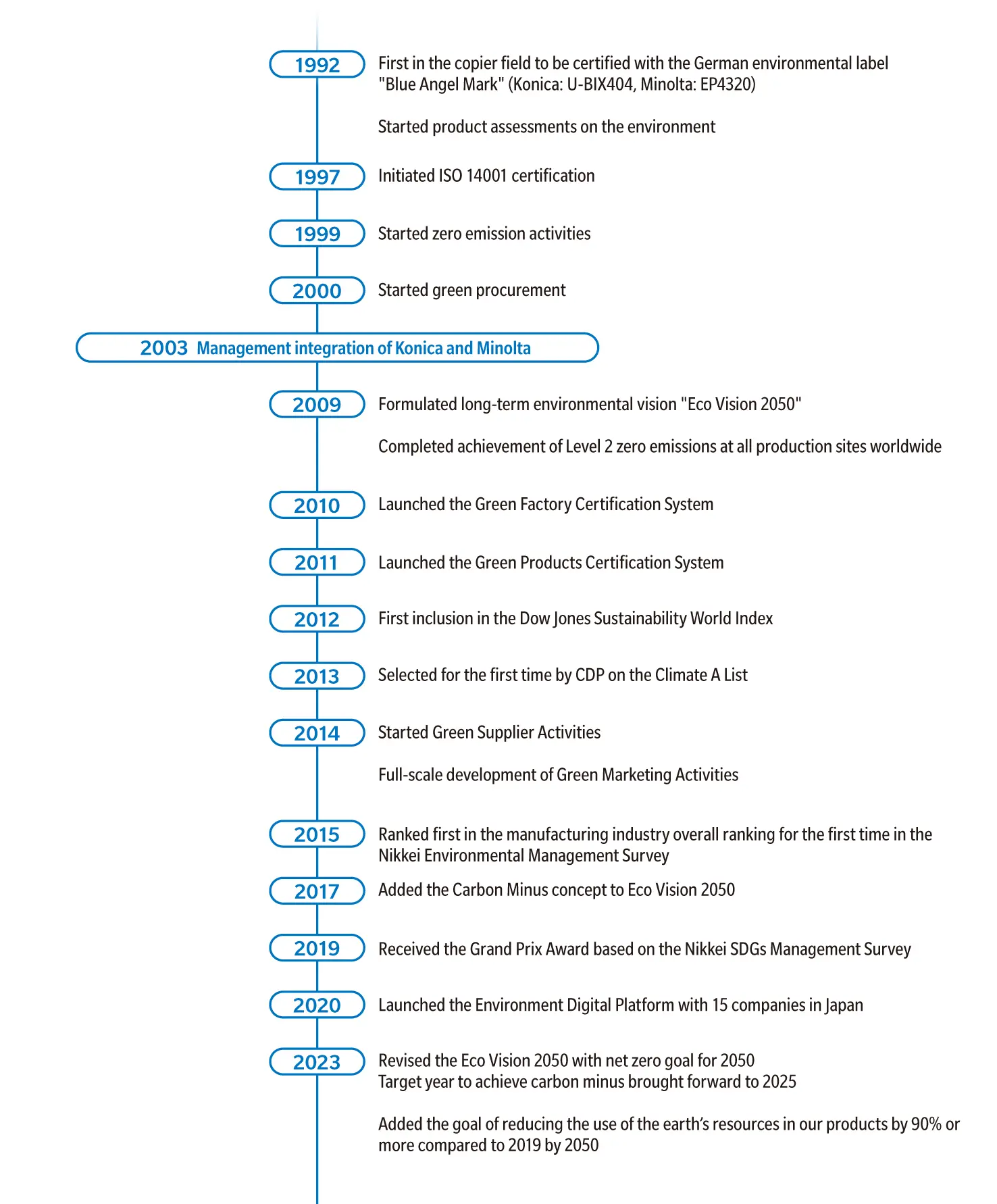