INNOVATION STORIES
SENSING
Originated from the Unique Light Measurement Technology of a Camera Manufacturer
Offering a Standard of Light and Color That Supports the Value Chain in Various Industries
- INDEX
Did you know that colors can be expressed as numerical values just like length and weight? Our color measurement solutions started with an exposure meter, which is used for measuring light intensity when taking photos. We started by developing an exposure meter to be built into a film camera. Then in 1964, Minolta released the View Meter 9, an exposure meter which was separate from the camera. This was followed by the Auto-Spot 1°, a high-performance exposure meter, which attracted the attention of the National Aeronautics and Space Administration (NASA). At NASA’s request, the Space Meter was developed by improving the Auto-Spot 1° to withstand the harsh environment of outer space. It was also installed in the Apollo 11 spacecraft, which made mankind’s first manned landing on the moon in 1969. The company thus contributed to the taking of photos in outer space, which captivated people at the time.
Our sensing business provides measuring instruments in the field of light and color based on photometric technology. Many companies use our products as standard tools in quality control processes for manufacturing displays and lighting equipment. We also offer essential products for color management in many industries, including automobiles, coating materials, plastics, textiles, construction materials, and food. Recently, we have expanded the scope of our business, continuing to underpin the value chain in manufacturing.
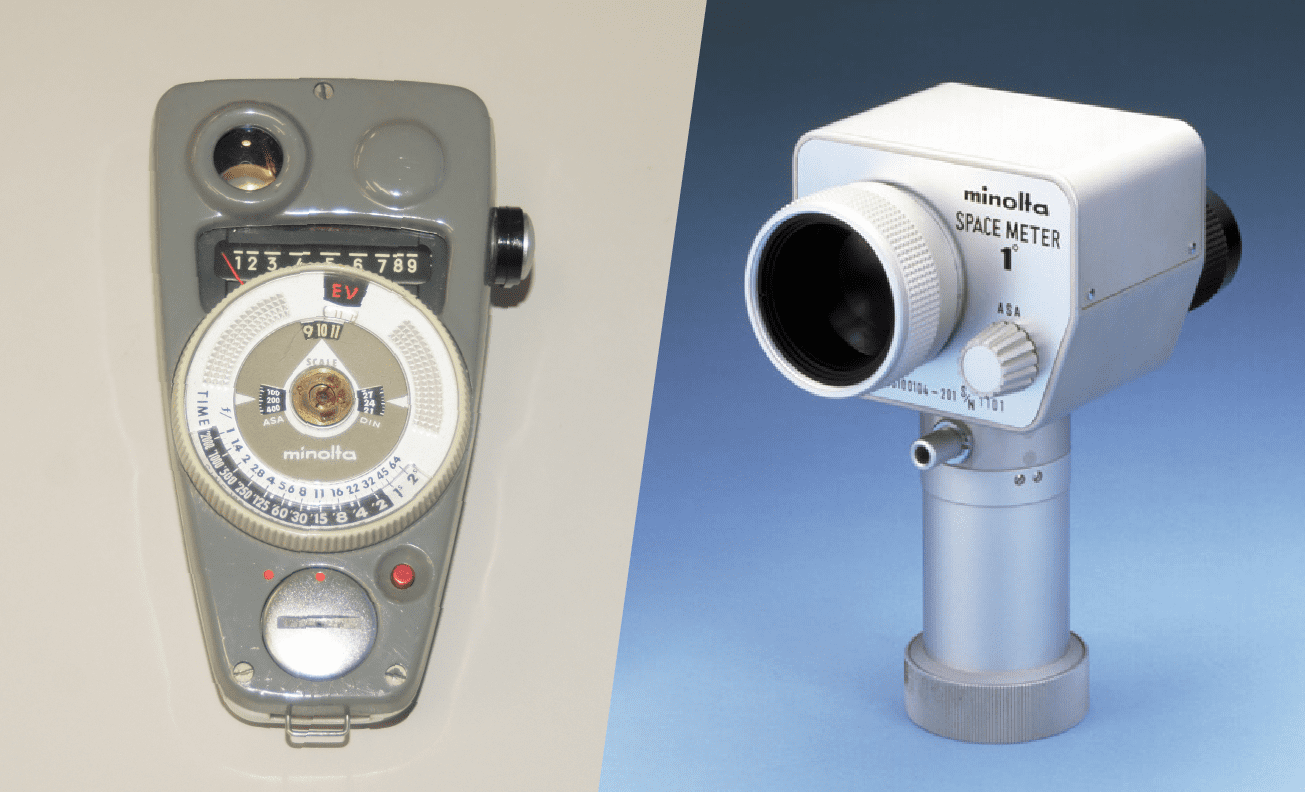
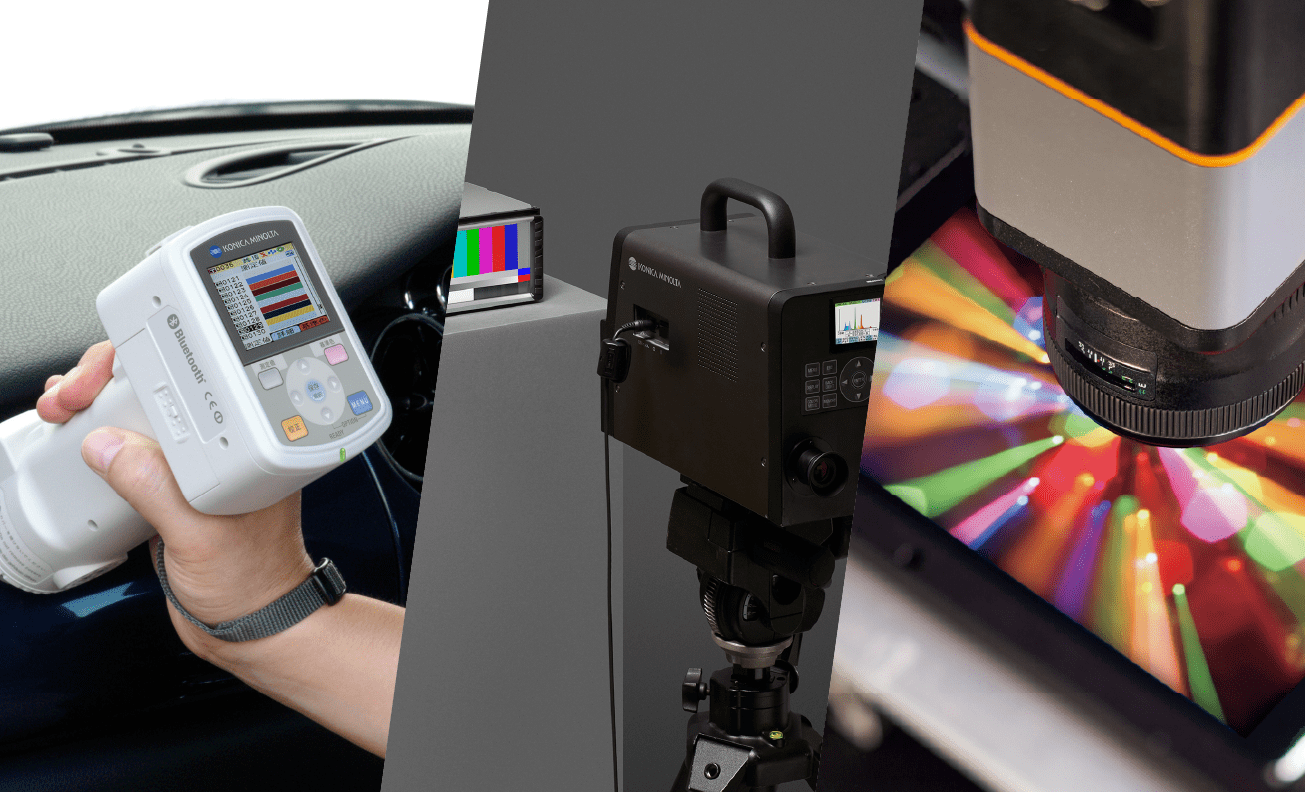
Engineering capabilities solving issues in the early days of color television
Our photometric technology, which started with an exposure meter, was extended to industrial measuring instruments in the form of the TV Color Analyzer in 1968. Development started following a request from engineers at Asahi Broadcasting Corporation in Japan, who wanted to show “correct white” on monitors. Color television broadcasting had just begun; all TV stations were struggling to calibrate the white balance of monitors, and many of them turned to using our product.
As the product gained a reputation for being effective for TV stations, we received requests from manufacturer s of electric home appliances to develop a measuring instrument for calibrating the color of cathode-ray tubes in the process of manufacturing TV sets. To enable TV programs viewed on color TV sets in living rooms to be perceived in the same colors as those on monitors for TV stations, color calibration was essential. As TV sets for general consumers were produced in far greater quantities than monitors for TV stations, we had to speed up and automate the color measurement process. We decided to reduce the measurement time by increasing the sensor’s sensitivity, build the measuring instrument into the manufacturing equipment rather than being hand-held by operators, and control its operation by computer. We succeeded in meeting these requirements, and thus the color analyzer for TV stations evolved into a product for manufacturing electric home appliances. This marked the beginning of measuring the color of light sources in the display manufacturing process.
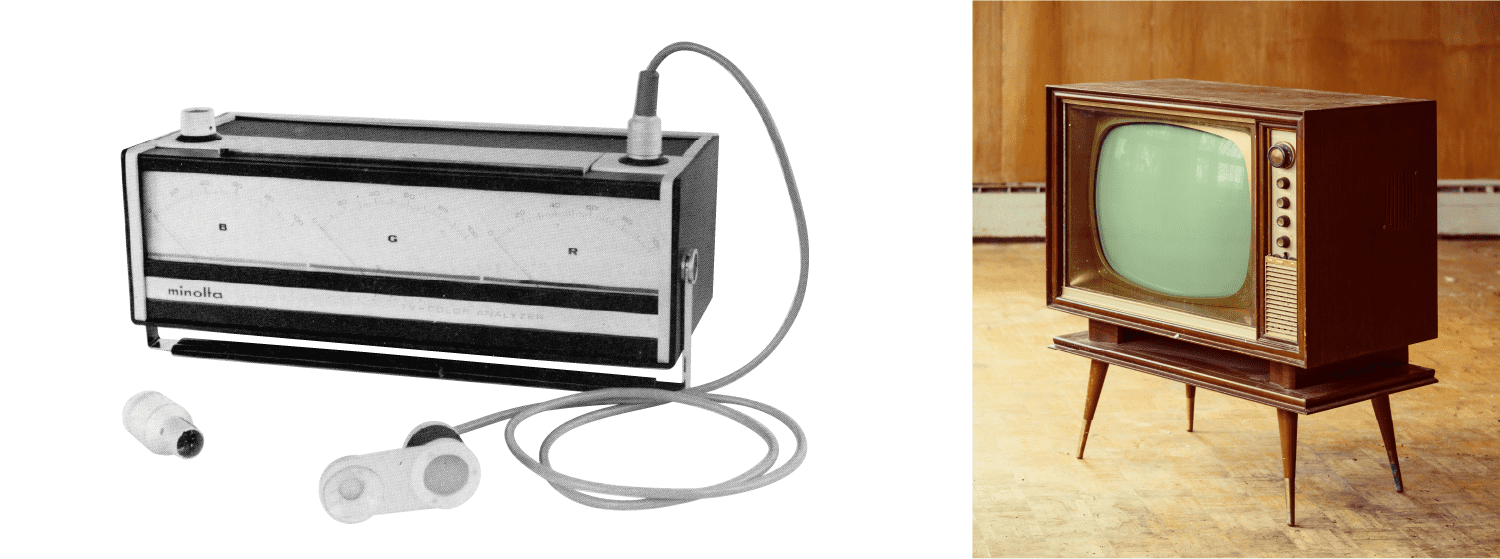
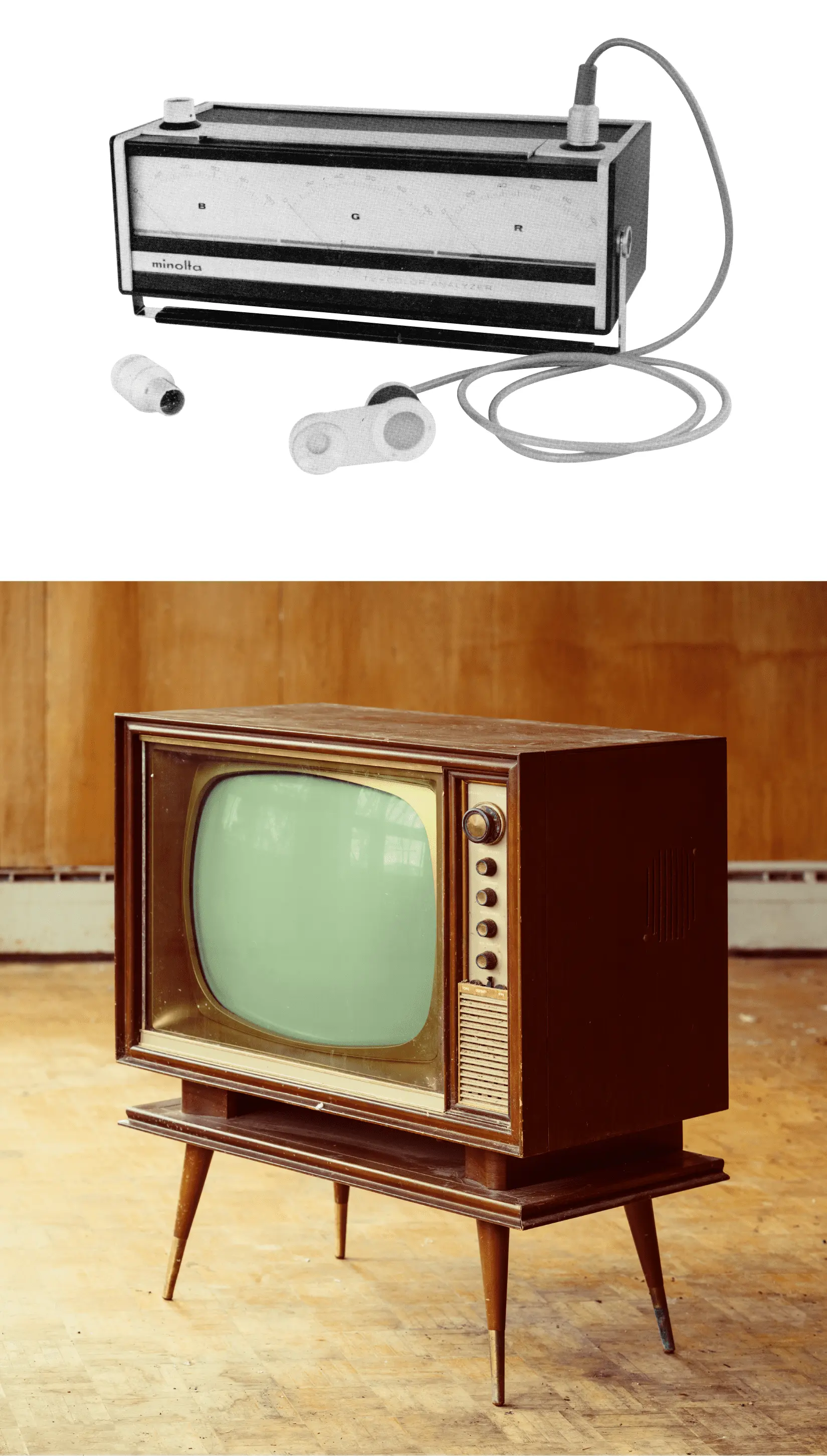
A turning point for light source color measuring instruments came with the advent of a new type of display. Around 1990, LCDs started to replace cathode-ray tubes, which had been the standard for TV sets for decades since the birth of television. Then, as they became thinner, LCDs spread from TV monitors to notebook PCs, mobile phones, and smartphones. Production of LCDs far exceeded that of cathode-ray tubes, and so demand for our products for LCD measurement, including the Display Color Analyzer CA-210, grew rapidly.
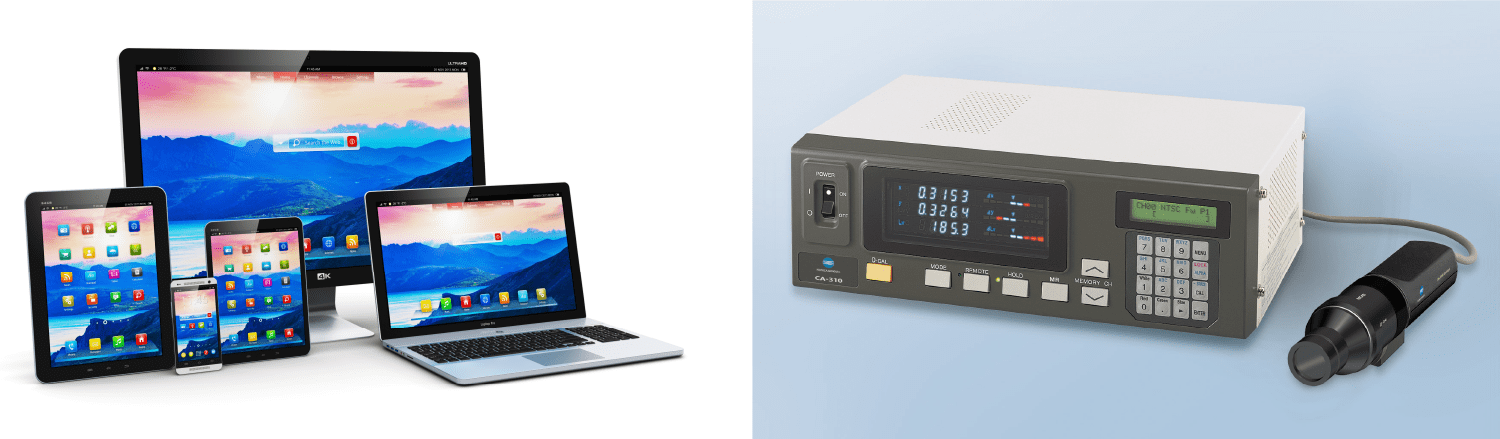
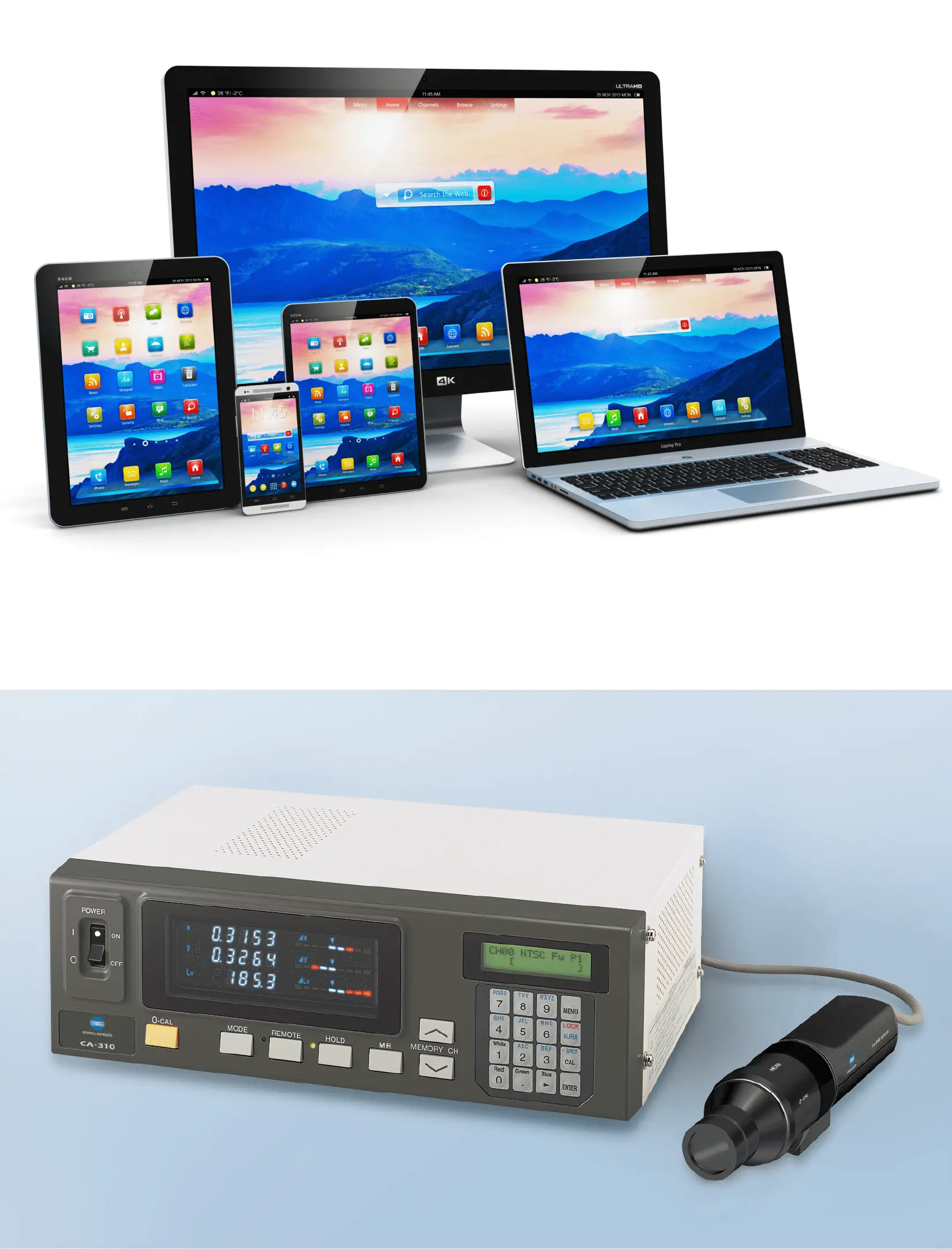
Later, organic light emitting diode (OLED) displays emerged. Unlike LCDs, which display images using the transmitted light from the backlight, OLED displays emit their own light. As a result, they can display a wide range of colors and properly render subtle differences in dark tones. To achieve high-speed measurement of differences in dark tones, the sensitivity of our instrument had to be improved dramatically, but this was a major challenge. Given that there was little scope for improving the sensor’s sensitivity, there were two possible solutions. One was to suppress the noise of the electrical circuit, and the other was to improve the optical system to transmit light to the sensor as efficiently as possible. Again, we drew on our strength as a camera manufacturer, and in 2007, we released the CS-2000, a spectroradiometer that could perform measurement as far as the super-low luminance range, to meet the new demand.
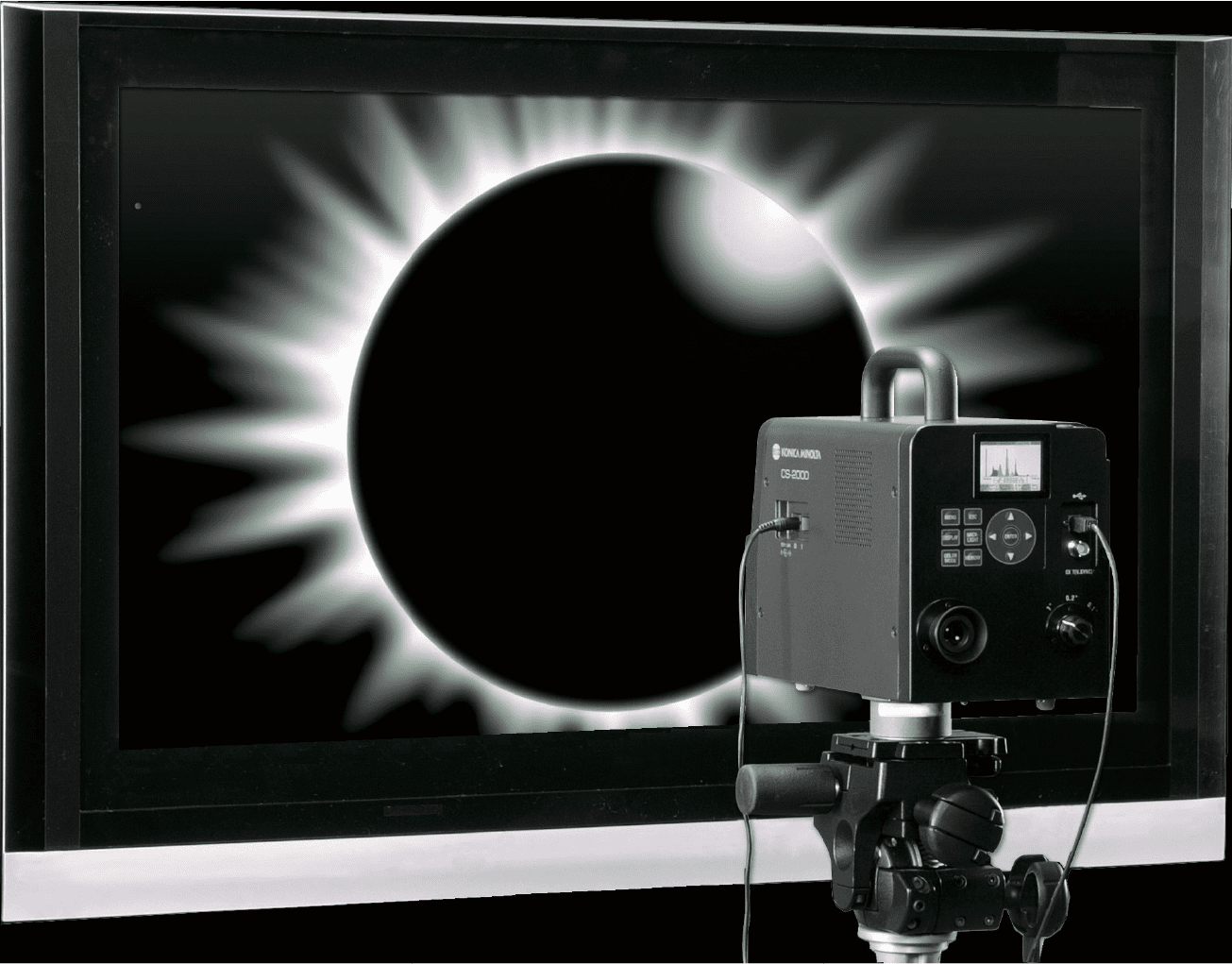
We continued to develop products to meet market needs, and today our share of the light source color measurement market for various types of displays is over 50%. We maintain relationships with many customers who are top brand companies, as well as companies who make up the value chain.
Color management in industry spreads thanks to compact, lightweight, handheld products
The color measurement of self-light-emitting devices, such as displays and lighting equipment, is referred to as light source color measurement. On the other hand, object color measurement measures reflected light by exposing a non-light-emitting object to light. The principle is the same as how humans perceive color. The light reflected by an object is received by a sensor—like the human eye—and the intensity is converted into a numerical value. Visible colors change depending on the light to which an object is exposed. As a camera manufacturer, we came up with the idea of casting light using a camera flash tube and then measuring color because a flash tube can generate light similar to daylight and thus produce colors similar to those seen in natural light.
Object color measurement can be applied to everything around us, including industrial products, clothes, printed matter, food, and cosmetics, in various states, including solids, such as metals and resins, as well as liquids and powders. The human eye excels at comparing colors, but there are differences among individuals and the processing speed is limited. Thus, object color measurement had the potential to be used in various industries.
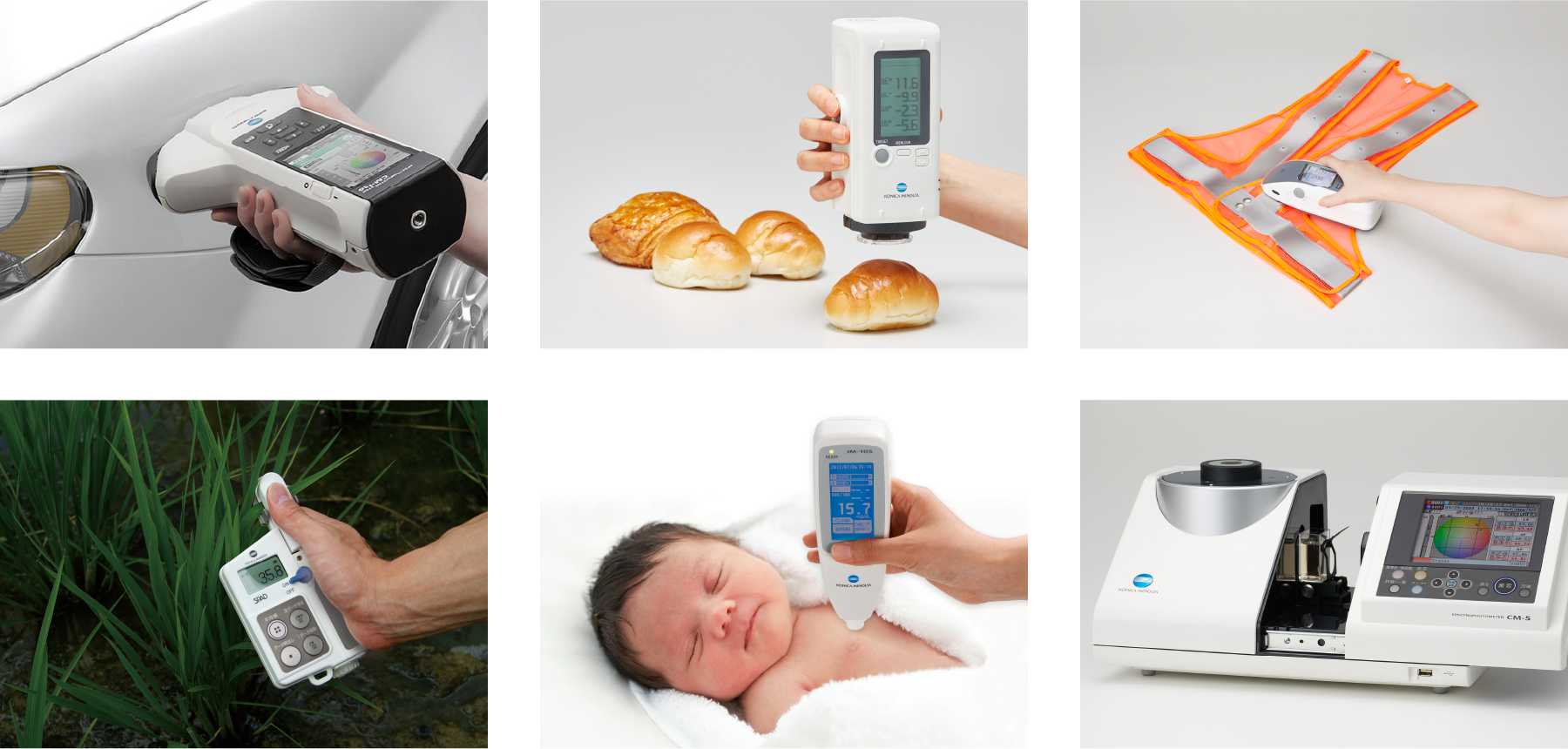
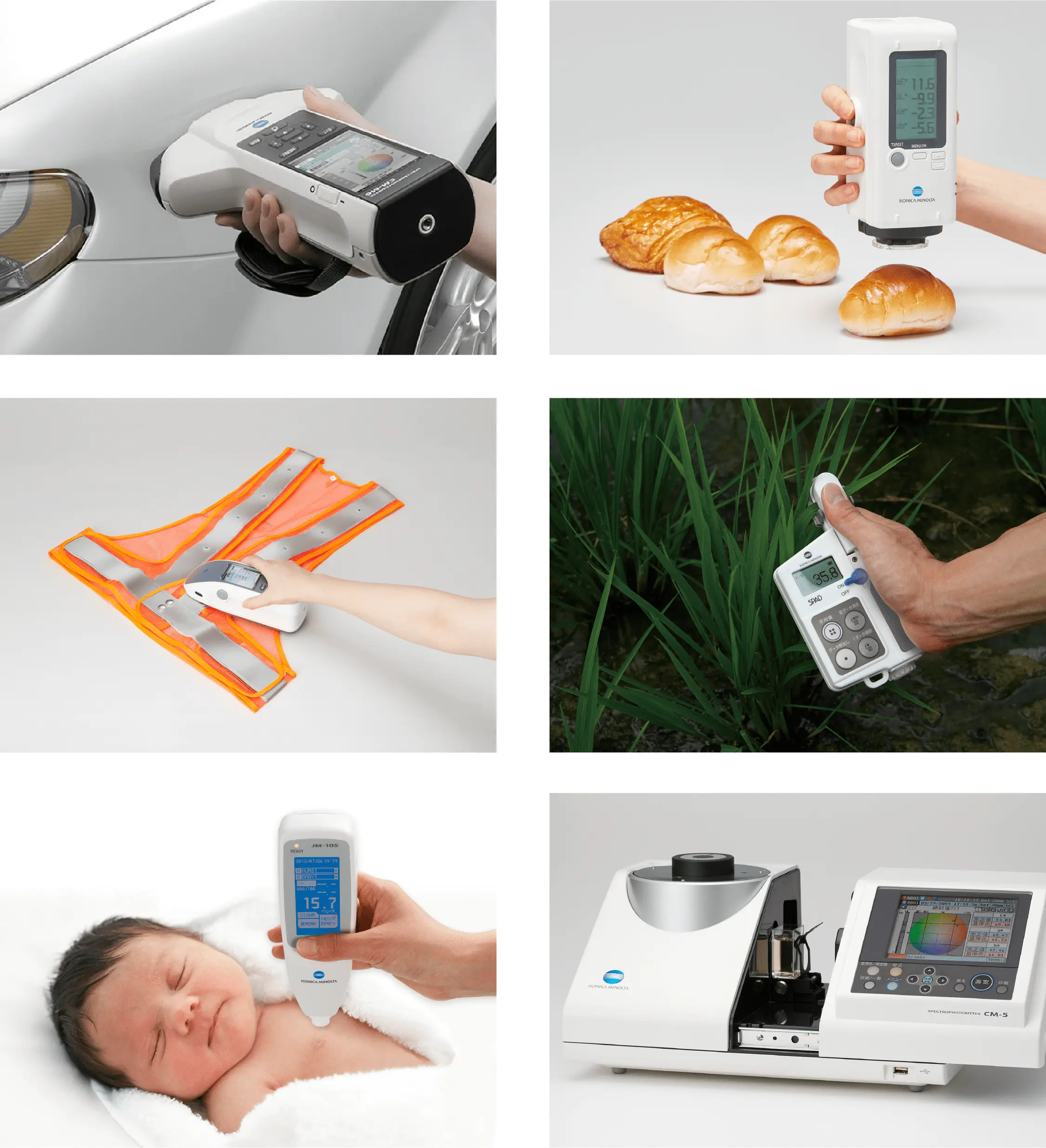
A typical application is automobiles, which requires color matching of parts made from different materials, including the metallic body and plastic fenders. Color management based on numerical values is essential to specify the colors to be used and ask supply-chain companies, including manufacturers of coating and other materials, to reproduce the same colors.
Color management is also important for food. The colors of vegetables and meat before processing are measured to manage the ripeness and freshness. The colors of bread and juice also serve as indicators of quality and taste.
We began developing an object color measurement product almost at the same time as the light source color measurement product. The Minolta Colorimeter, which was released in 1980, helped us enter the object color measurement business. The product was designed to measure both light source colors and object colors. Two years later, in 1982, the Chroma Meter CR-100, which was designed exclusively to measure object colors, was released. This revolutionary product was compact, lightweight, and handheld. Measuring instruments at the time were large and typically required items to be measured to be taken to a laboratory or quality inspection room. In contrast, our handheld measuring instrument could be taken to the site for easy on-site measurement of even large or heavy items. We were able to design a compact and user-friendly shape thanks to our unique strengths as a camera manufacturer. Color measuring instruments became popular in various industries, and our sensing business grew accordingly.
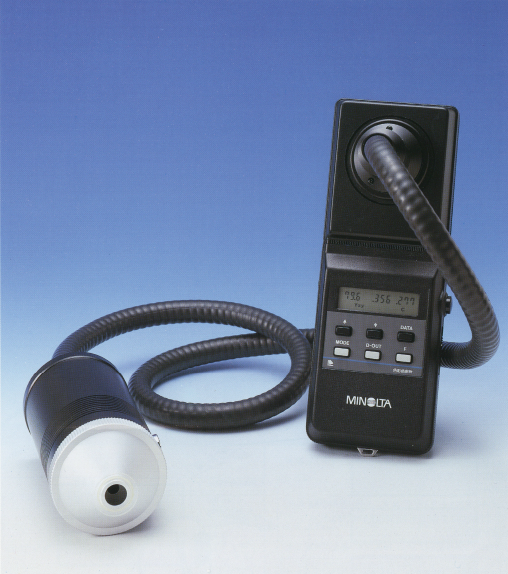
The global deployment of these measuring instruments was made possible by our global network originally created for cameras and copiers, and the instruments were accepted by global customers for their reliability.
Color management is needed in various industries, but there are still many customers who have not used measuring instruments. We have a duty to give in-depth explanations of the principle of color measurement and how to use measuring instruments to new customers through exhibitions and webinars, and to contribute to DX in various industries.
De facto standard established based on mutual trust
In the 2010s, the sensing business started to undergo a major transformation. As we sought solutions to expand our business, we embarked on large-scale mergers and acquisitions. The industry was characterized by frequent mergers, and market shares were starting to change due to mergers between competing manufacturers.
We acquired Instrument Systems GmbH, a leading German manufacturer of lighting measuring instruments, in 2012, and then acquired Radiant Vision Systems, LLC, a U.S. display inspection systems manufacturer, in 2015, thereby reinforcing our foundation in the light source color measuring instruments industry.
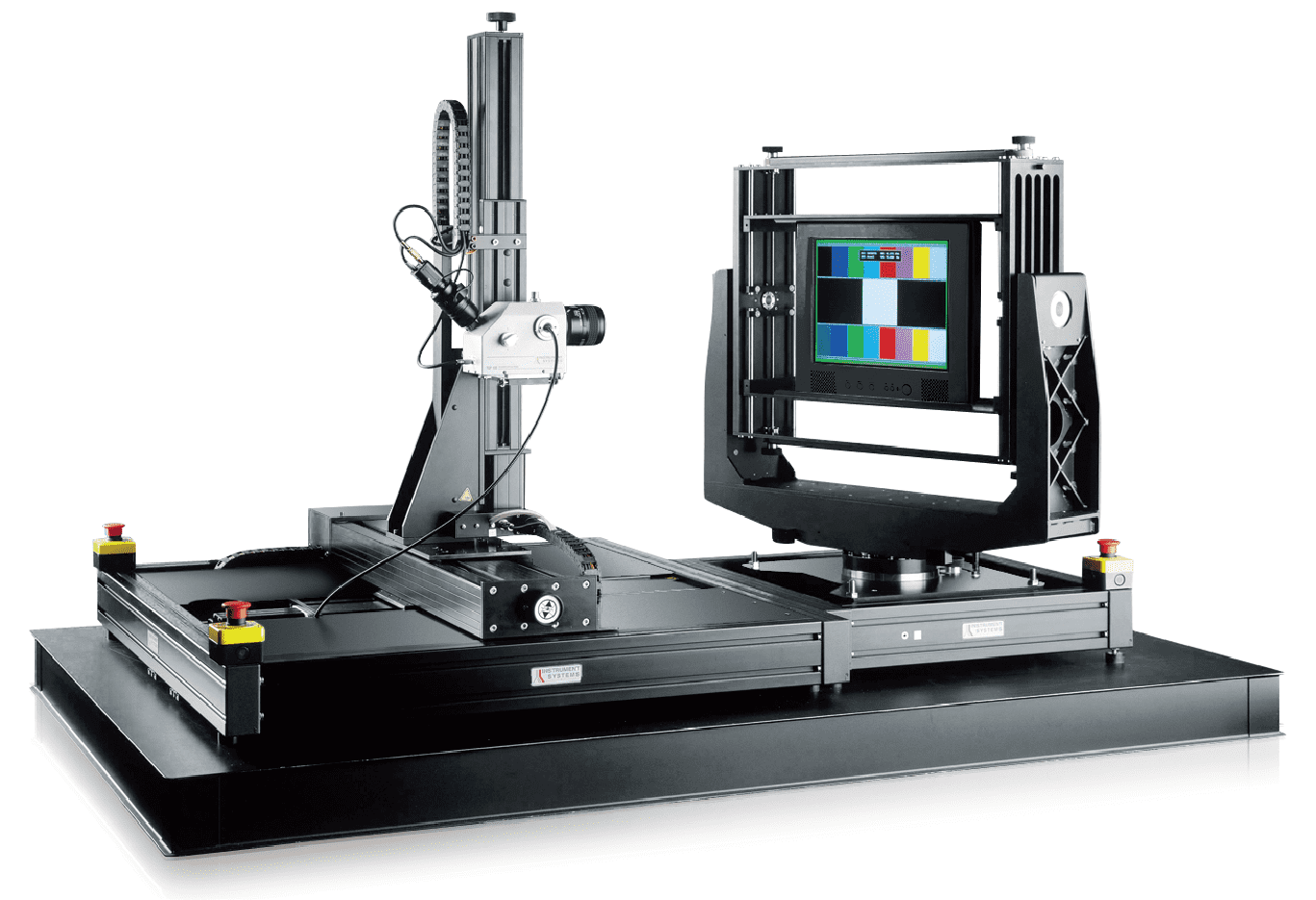
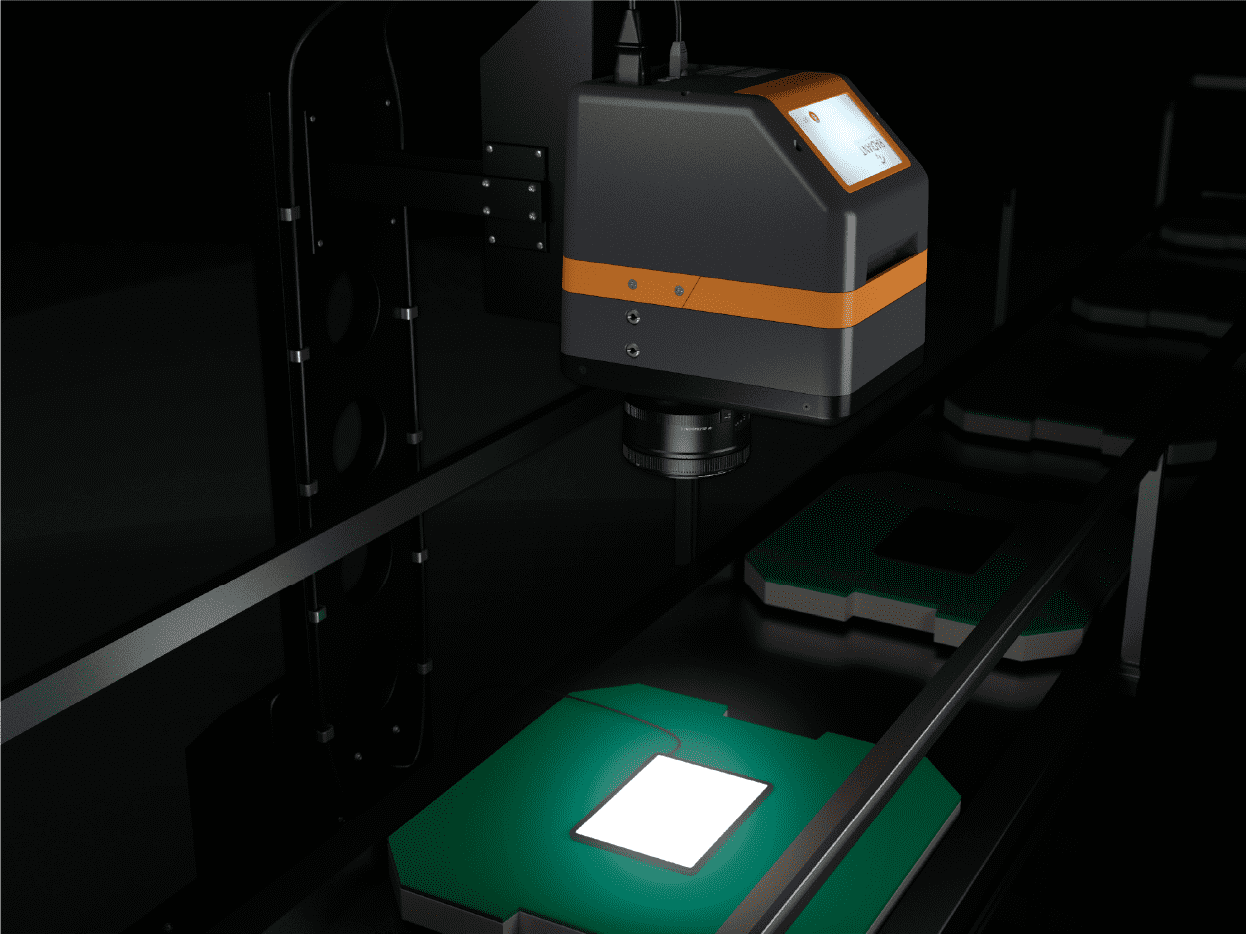
Instrument Systems manufactures high-accuracy products that are the global standard for light source color measurement and are highly evaluated worldwide. The company is also renowned for its outstanding human resources: two thirds of its employees, including development and sales staff as well, have a doctorate. Meanwhile, Radiant Vision Systems is a leading manufacturer in the display inspection market and develops customized systems to meet customers’ needs. In particular, it has deep expertise in software development. The person in charge at Konica Minolta commented, “I felt tense even when talking with them as equal partners in meetings; I greatly respect them. We have a lot to learn from them, including how they communicate directly with customers, gain their trust, and determine the specifications together.” We have built mutual trust as partners that inspire each other beyond the relationship between a parent company and subsidiaries.
Later, two other companies joined the Konica Minolta Group: Eines Systems S.L., a Spain-based leading company in the automotive visual inspection market, in 2019, and Specim, Spectral Imaging Oy Ltd., a Finland-based leader in hyperspectral imaging, which involves conducting measurements at wavelengths invisible to the human eye and detecting components of materials and other information, in 2020.
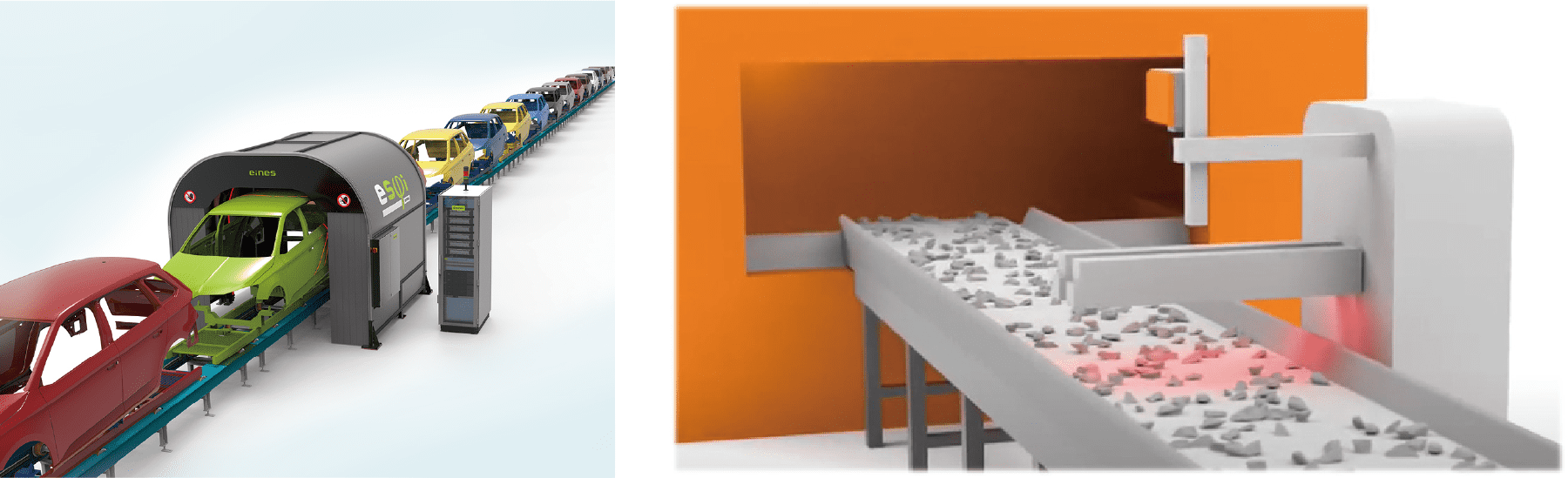
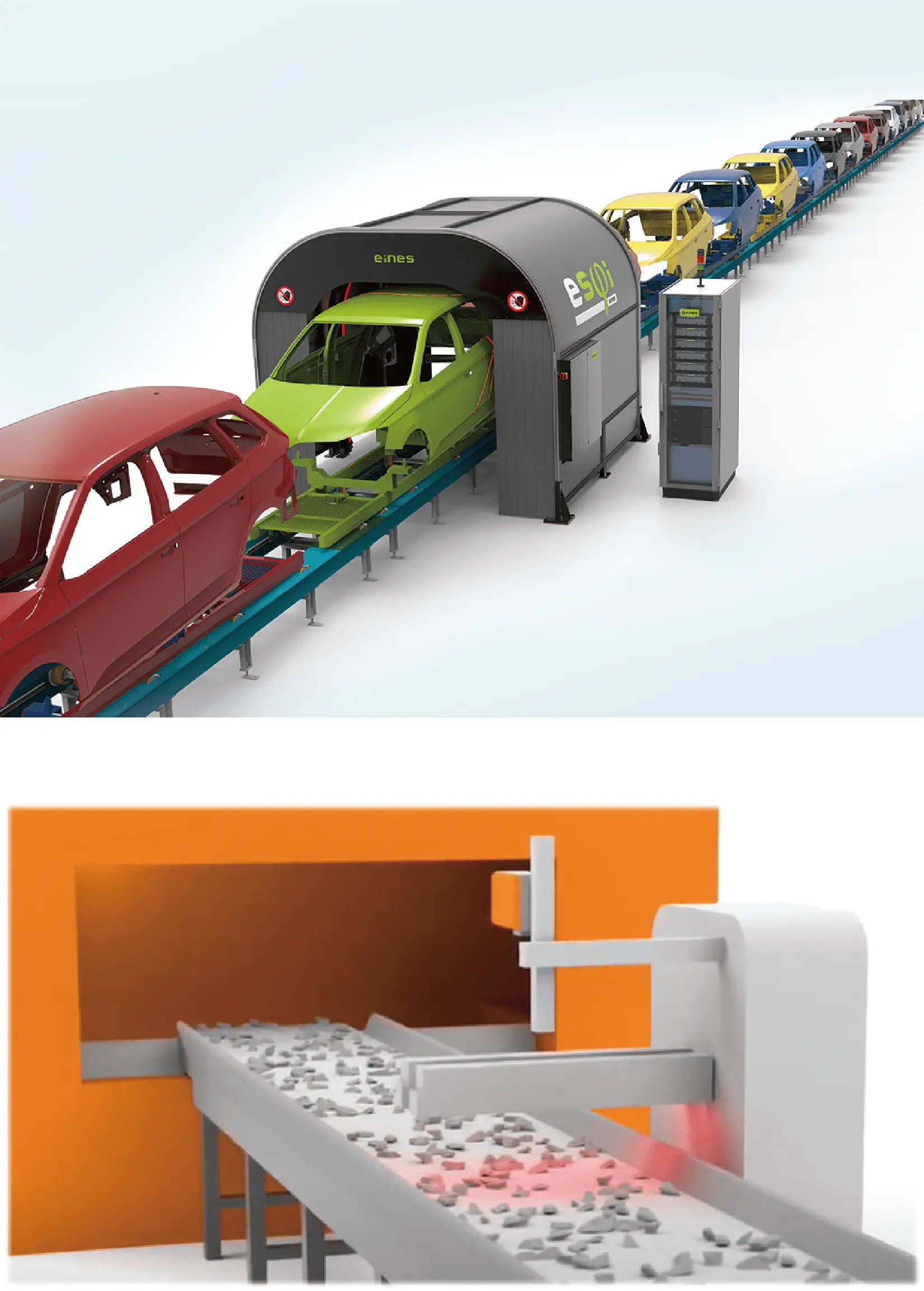
For more than 50 years since starting to develop color measuring instruments, we have continued to create products that meet customers’ needs and have expanded the scope of our business, becoming the de facto standard in many fields.
Our reputation is founded on a track record of delivering accurate measurement results for decades. We have gained trust based on minimal deviation of values measured by instruments and instrumental errors when conducting measurement using multiple instruments. We also have sophisticated calibration technology for performing calibration and comparing values with the standard. We have added renowned companies in the measurement industry to our group thanks to our devices’ reputation for reliability among global customers.
Mutual trust with customers is a critical asset. As measurement targets and needs continue to change and diversify with the times, we will continue to develop technologies that fulfill customers’ needs and contribute to the global value chain.
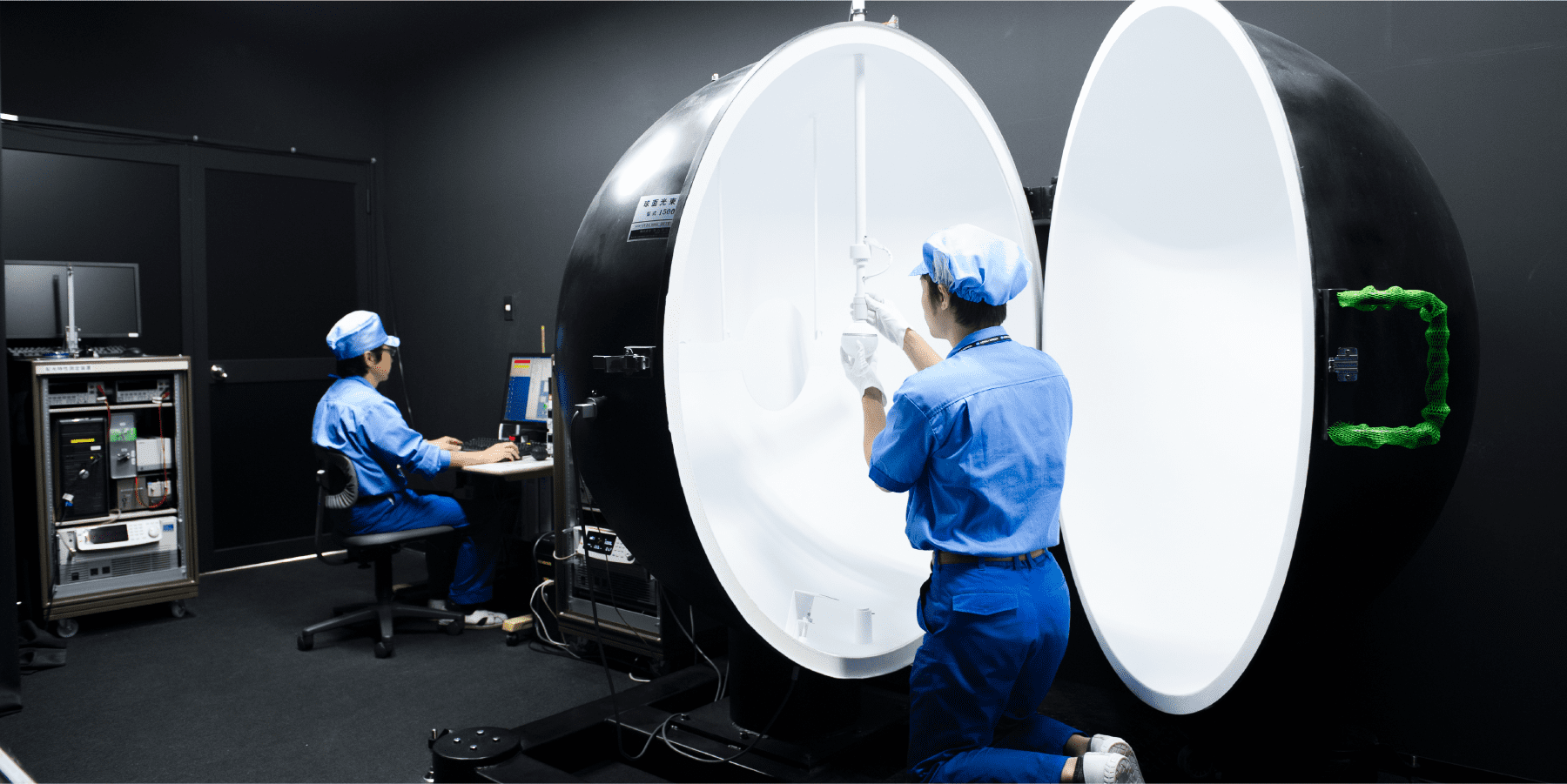
In the interest of clarity, “Konica” and “Minolta,”—the trade names that were used before the merger that formed “Konica Minolta”—are used throughout this text. Each company underwent a number of name changes throughout their history.
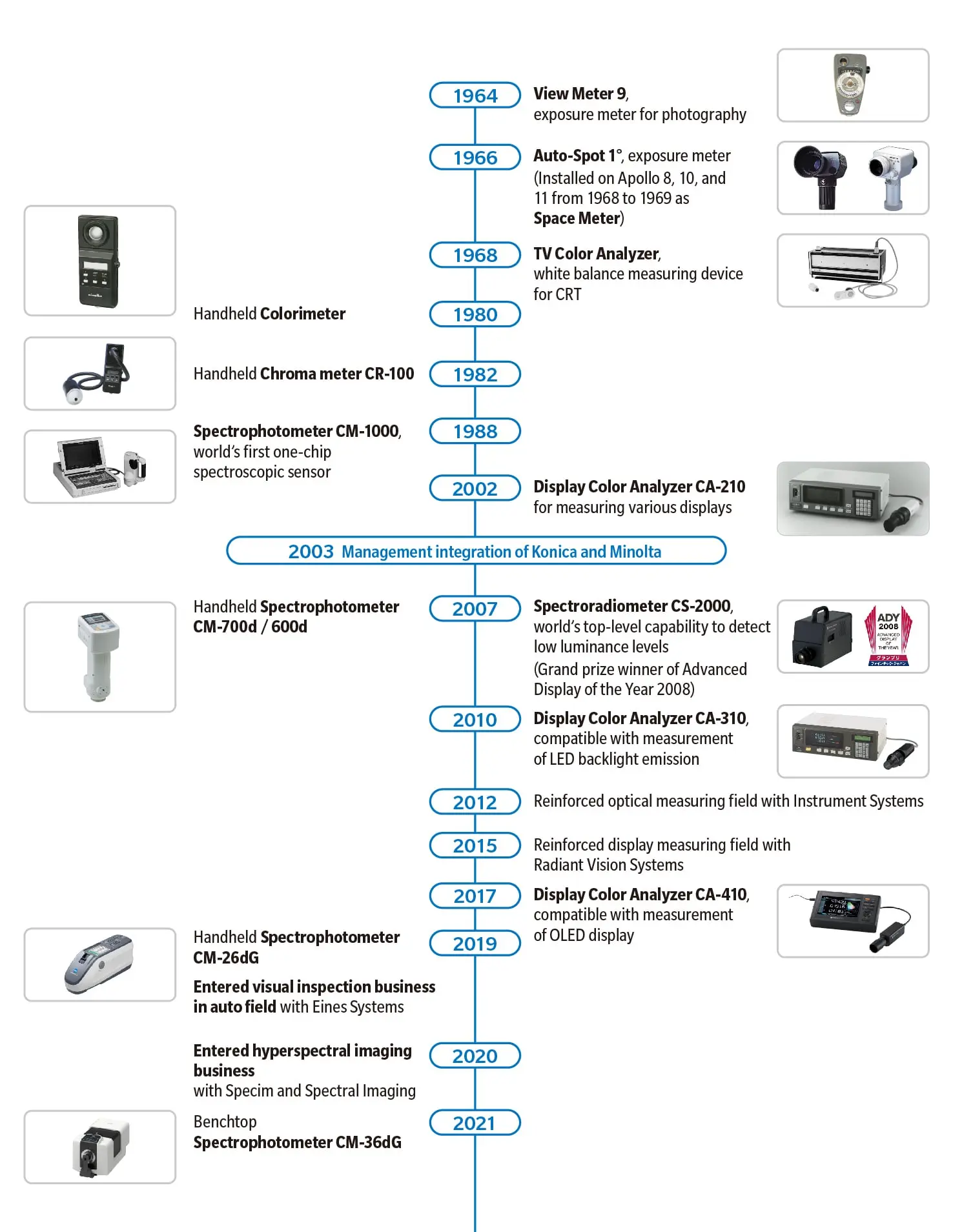